付属屋社長が製造現場を行くシリーズ。
今回(2019年4月)は和歌山県にあるボタンメーカーの株式会社タカオさん(以下敬称略)に訪問。このタカオは当社の仕入先であるルックウェルさん(以下敬称略)の子会社です。ポリエステルのボタン製造を中心に行なっています。製造現場はもちろんのこと、なぜ和歌山にボタンメーカーが多いのかなど歴史の話とともにご紹介していきます。
※株式会社ルックウェルは2022年3月に廃業しています。
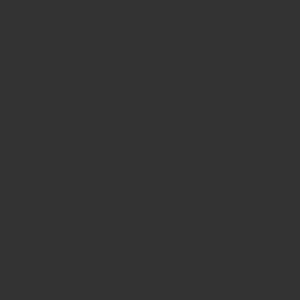
和歌山の南紀白浜へ
羽田空港 7:25発の早朝のフライトで和歌山県の南紀白浜空港へ。かなり小さな飛行機で片側2列の4列シートです。早朝便に関わらずほぼ満席。南紀白浜までは1時間ほどのフライト。羽田では曇り空でしたが南紀白浜空港に着くと大雨。
ここからレンタカーを借りて上富田町にあるタカオへ。海岸沿いからやや内陸の方へ20分ほど走ると到着。着いた頃には雨も上がっていました。
ボタンの産地、和歌山
タカオに着くとルックウェルの社長でもある松本社長が出迎えていただき、会議室でまずはお話を聞くことに。顧問である小林さんも同席してくれて貴重な昔話を聞くことができました。
和歌山にボタンメーカーが多いというのはの知っていましたが、それが何故なのかは知りませんでした。今回、小林顧問の説明でその理由がわかりました!
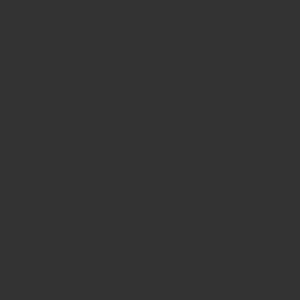
もともとボタンの加工は大阪が発祥で、貝や水牛などを輸入してきてボタンに加工をしていました。ルックウェルも大阪で貝ボタンの原料である原貝の輸入などをする貿易会社だったとのことです。大阪の近隣である和歌山県や奈良県で農業をしている人が閑散期に出稼ぎで大阪に行き、ボタンの加工工場で働くようになりました。そして、大阪の資産家がボタン加工技術を持つ人の多い和歌山県や奈良県にボタン工場を作ったのが始まりだそうです。
和歌山県ではタカオのある上富田町がボタン工場発祥の地で、そこから隣の田辺市にも広がっていきました。大きな規模のボタン工場もでき、そこの下請け加工をする町工場や家内工業も増えこの地がボタンの産地となりました。
今はピーク時の1/5の生産量になってしまい廃業する工場も多いです。日本で和歌山以外ではボタンメーカー最大手のアイリスさんのある群馬県や香川県などが産地として挙げられます。今の和歌山の南紀白浜地区ではボタンよりも梅加工、加工食品が主要生産品になっています。
ポリエステルボタン製造現場
タカオではポリエステルボタンの製造をしています。そのポリエステルボタンの製造現場を見せていただきました。ちなみに貝やナット、水牛などの天然素材のボタンはルックウェルのフィリピンの工場で加工しています。
ポリエステルボタン製造方法
まず、基礎知識としてポリエステルボタンの原材料は大きく2種類あります。ひとつは棒菅成型法による棒材というものです。もう一つが遠心成型法による板材というもの。ボタンのデザインによって原材料は変わってきます。水牛調、ナット調のデザインは棒材を使用し、貝調や層になるデザインには板材を使用します。
棒材の製造工程
棒材の製造工程はアルミの1mほどのパイプにポリエステル樹脂を流し込んで作成します。縦に並べたパイプに出したいデザインの柄の樹脂を流し込む訳ですが、この流し込む柄は企業秘密です。液体状で流し込んだものが固まると水牛やナットの柄になるので不思議です。この原材料づくりは見事な職人技なのです。
パイプに流し込んだものが固まるとパイプから出します。出してすぐはゴムのように弾力があり、黒い柄だとウナギのよう(笑)熱をかけて硬化させていきます。
固まった棒材を輪切りにし切削機で削りボタンにしていきます。同じ原料で作った棒材は金太郎飴のようにどこをとっても同じデザインが出てきます。切削の工程から先は棒材も板材も同じです。
板材の製造工程
板材は液体状のポリエステル樹脂をドラム式乾燥機のような機械に流し込み作ります。ドラムが回転することで遠心力で樹脂が均等に壁面に張り付き硬化して板状の原料になります。貝調のポリエステルボタンは貝のパール調の光沢を表現するためにパールを入れます。このパールが遠心力で立つことにより綺麗な光沢を出すことができます。逆にいうと棒材では貝調ポリエステルボタンは作成できません。
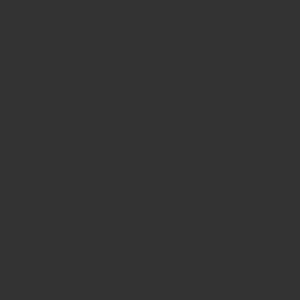
出来上がった板状の材料をパンチングという工程で丸く抜いていきます。これを次の切削工程でボタンの形状(タブレット)にします。
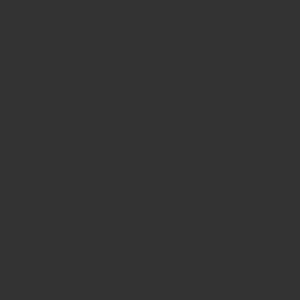
切削と研磨(艶出し、艶消し)工程
タブレット状になった原料を切削機に入れ、削っていきます。タブレットの方が固定され、そこにカッターの歯のようなものが回転し、縁を作ったり、穴を開けたりしてボタンの形状にしていきます。
削った後は加車と呼ばれるドラムに研磨剤と一緒にボタンを入れてバリをとったり、ツヤ出しをしたり、ツヤ消しにしたりします。
中に一緒に入れるのは石だったり、竹だったりします。
ツヤ、ツヤ消し、半ツヤとフィニッシュングは変えることができます。タカオでは特にムラの無い綺麗なツヤ消しに定評があります。
ちなみにこの加工に半日以上を費やします。無理言っていつも早く上げてもらっていますが、かなりの手間と時間が掛かっていることを改めて実感します。
検品
最終工程の検品です。上がってきたすべてのボタンを目視で全量検品します。しかも二人がかりです。
わざと部屋を暗くし、手元部分を明るくして検品します。かなり地道で根気のいる作業です。しかし、こうすることでB品がまったく無い品質のいいボタンを提供しているのです。海外のボタンメーカーとの大きな違いのひとつがこういうところに手を抜かないことです。日本メーカーとしての誇りを感じます。
今回の製造現場訪問レポートはまずはここまでとして、続きで松本社長、工場長へのインタビューを含めてお送りします。
付属屋社長が製造現場を行くシリーズ、前回の続きです。当社の仕入先であるルックウェルさん(以下敬称略)の子会社で和歌山県にあるボタンメーカーの株式会社タカオさん(以下敬称略)に訪問(2019年4月)。前回は和歌山のボタン産業の歴史からポリ[…]
記事、ボタンに関するお問い合わせはこちらから。
お問い合わせ
【追記】
今回、ご紹介したルックウェル、タカオは、既に会社・工場ともに閉鎖されております。